I’m not done yet!
Here’s my brief hello and happy new year to all you my readers and followers! I felt like posting this update to share that although it’s been a quiet year for this blog, I’m by far not done DIYing :)
2018’s been a weird one for me in that I’ve done more DIY than ever, but none of it was anything to write about. Among many other things all my DIY included a kitchen which (perhaps at its low point) looked like this:
..and come to think about writing, well, I wouldn’t have had the time for it anyway; at the busiest of times I was pulling 14-16 hour days for weeks on end to get things sorted. But happy to have survived and that’s that.
Despite the blog’s been dead this year, I’d like to also send thanks to everyone who kept checking back and getting in touch throughout the year for quick advice, details about my builds, left comments in posts and what have you. I may have not been the fastest at responding to mails etc, but I did manage eventually.
May 2019 turn out better with having the time for new, blog-worthy DIY builds :)
Thanks & Happy New Year!
LED mod for Lego Star Wars Slave 1
To wrap up 2017 here’s the near-mandatory, and-now-for-something-completely-different, holiday seasons DIY post.
This time around though I’m skipping the turkey in favor of adding LED lighting to thruster engines of Lego Star Wars Ultimate Collectors Set (UCS) nr. 75060 aka ‘Slave 1’.. Aka ‘that clothes iron looking spaceship’ with which Jango & Boba Fett transport their *preciousssss* bounty in in Star Wars movies. Read More…
ProtoTypo PT7 – CMY
Here’s a small mod for Fonitronik Cascade, a 4HP eurorack module that allows mixing, attenuating / inverting and offsetting of three separate input signals (later “channels” or “ch.”). I totally love it for the size, features and price.
The mod brings on-board jumper terminal JP1 to front panel, so that the signal routing behavior of Cascade can be changed without removing the module from eurorack case.
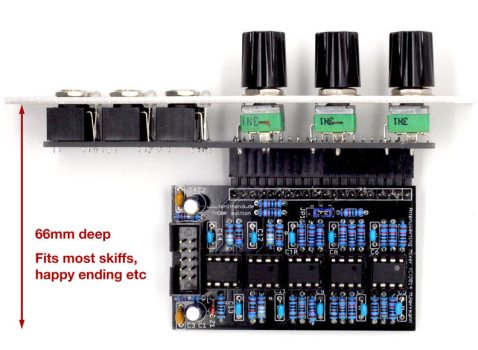
Fonitronik Cascade, JP1 (with blue jumper) next to the board interconnect. Photo by Thonk.
Eurorack Monster Base, the build
If you found this post via a web search by all means do check out my previous post about the design of this build. You know, to give more context to all the hands-on, wing-it-as-you-go build stuff that’s about to follow!
This build is a Doepfer Monster Base inspired large eurorack case with a few bays for 1U 19″ rack modules! I’ll start with.. Read More…
ProtoTypo PT6 – MCV4E
ProtoTypo PT6 is a straightforward conversion build of a Doepfer MCV4 into a eurorack module. I just removed the circuit board from original case, made a matching eurorack panel and gave that some fffuuuugly artwork! Not much to the build so I figured maybe I’ll just run through my magnificent paper sticker panel artwork method \:D/
Recent Comments